Weight packaging machines
Automatic Weight Packaging Machine – Model THV-2025PV-B Continuous Packaging System – High Performance Around the Clock! We offer you an exceptional packaging machine, designed to the highest international standards to meet the demands of the modern food industry. This machine represents an ideal industrial solution for packaging snack products such as chips, potato chips, seeds, nuts, and other dry goods with precision, speed, and consistency. The machine is fully servo-driven, eliminating any traditional mechanical systems, which results in significantly reduced breakdowns and maintenance, increased operating life, and impressive performance stability. Exceptional features that make this machine the best in its class: ✅ Continuous packaging with a conveyor continuous system for non-stop production. ✅ High productivity ranging from 90 to 120 packets per minute (depending on weight). ✅ 14 highly sensitive and accurate scales from High Dream. ✅ PLC control unit from Taiwanese company Delta – immediate response and impressive operating accuracy. ✅ 7-inch DELTA touch screen – comprehensive and easy control of all machine functions. ✅ OMRON high-precision temperature control system – fully adjustable from the screen. ✅ Automatic roll feeding system and intelligent compensating motor with roll end alarm. ✅ 304 food-grade stainless steel exterior, easy to clean. ✅ Completely free of mechanical complexity – relying solely on servo and stepper motors, making it virtually maintenance-free. Why choose this machine? ⭐ Because it's built to last – durable and robust, it can withstand harsh operating conditions around the clock. ⭐ Because it operates smoothly without any sudden downtime or breakdowns. ⭐ Because it relies on advanced servo technology, ensuring the highest weight and filling accuracy. ⭐ Because it gives you flexibility in adjusting size, weight, roll length, and production sequence. ⭐ Because it's operator-friendly – easy to operate with a smart and simple interface. Included parts: 🔹 Feeding conveyor with tank and vibrator – intelligent product feeding. 🔹 Conveyor belt for finished packages. 🔹 Date printer. 🔹 Weighing device mounting platform. Technical specifications: ⚙️ Electrical power: 5.75 kW – 380/220 V – 50 Hz. 📐 Dimensions: Length 500 cm – Width 300 cm – Height 420 cm. 🆔 Model number: 001-2025 Why choose Al-Huda? Because Al-Huda is not just a manufacturer, but a reliable industrial partner that prioritizes quality and precision. We have extensive experience in manufacturing packaging lines and are committed to providing machines that combine European technology with high operational efficiency. Al-Huda is proud that this particular model, the THV-2025PV-B, has become the first choice for food factories seeking to improve efficiency and reduce breakdowns, thanks to its fast, accurate performance and high stability. Choose Al-Huda... because quality starts here. A comprehensive and detailed text has been written for the Continuous Weight Packaging Machine, focusing on strength, durability, ease of operation, and Al-Hoda's expertise. You can now review the text in the sidebar. Would you like me to convert it to a Word file for download and printing?
parts
1. Packing and packaging machine for all kinds of chips - seeds – nuts
2. The entire working system depends on 0075 KW motors and gearboxes to control the scraping +0.75KW to control the jaws
3. Roller width used: as per customer request
4. Maximum roll length 320mm
5. Production capacity 60-70 packages / minute, depending on the weight
6. Advanced PLC control system with quick response from DELTA company
7. 7 inch electronic touch screen from DELTA
8. High precision machine temperature control system from (OMRON) The temperature can be controlled from the screen
9. The machine is equipped with a stepper motor to move the roller bearing saddle in a way that is controlled from the screen
10. The machine is equipped with a stepper motor to compensate for the pull of the roll, in addition to alerting the operator about the end of the roll
11. The machine is equipped with safety sensors for the safety of the operator
12. The machine is equipped with a daily and comprehensive production and control counter
13. The external structure of the machine (STAINLESS STEEL 304)
14. All parts of the machine that come into contact with the materials to be filled STAINLESS STEEL 304
15. Roll forming device, Italian model, according to customer request (1 pcs), easy to replace
16. The type of roller used for the machine (embedded cellophane)
Accessory Parts
1 - STAINLESS STEEL 304 STRAP
(PVC letter Z) with tank, vibrator, control circuit and electronic sensors to feed the machine with the product automatically.
2- Conveyor belt for ready-made packages
3- Date printer according to customer's choice
4 - HIGH DREAM's Smart Weighing Set with Combination System
5- A platform for installing the STAINLESS STEEL 304)

Continuous packaging machine - Continuous system
🔹 It is the heart of the production line, forming, filling, and wrapping bags automatically and continuously, ensuring high productivity and optimal work efficiency.
🔍 Detailed explanation of the mechanism:
1️⃣ Automatic Bag Forming
The nylon is pulled from the film roll and thermally formed into a ready-to-use packaging bag.
2️⃣ Automatic Filling
The bag is directly filled with the desired material, whether granules, chips, powder, or various food products such as chips or half-fried potato fingers.
3️⃣ Closing and Packaging
The bag is sealed using precise thermal systems, then automatically separated, and the process begins again continuously without interruption.
⚙️ Technical Specifications:
🔸 Operating System: Continuous System - No downtime between cycles
🔸 Production Speed: Over 130 bags/minute (depending on product type and weight)
🔸 Control System: Equipped with a smart PLC control panel with a highly sensitive touch screen
🔸 Drive System: Driven entirely by high-precision servo motors
🔸 Machine Body: Made entirely of food-grade 304 stainless steel
🔸 Packaging: Hot Sealing System
✅ Machine Features:
🌀 Continuous System - High Efficiency and Ultra-Fast
⚡ High Production Speed of Over 130 Bags Per Minute
🛠️ Easy to operate and maintain, designed to suit industrial work environments
🧠 Equipped with an advanced control system that facilitates precise machine operation and monitoring
🔒 High safety system with smart sensors to protect the operator and product
🏭 Designed According to the highest standards of quality and industrial craftsmanship.
🍽️ Ideal Uses:
Packing all types of chips (corn, potatoes, pellets, etc.)
Packing half-fried potato fingers
Packing dry food products: sugar, salt, spices, powder, flavors, grains, nuts, etc.
Can be connected to multiple packaging systems: electronic scales, volumetric scales, screw caps
🎯 "An integrated packaging solution - speed and accuracy in every bag"
The continuous packaging machine with the continuous system is the ideal choice for modern production lines, combining high performance, continuity, ease of operation, and manufacturing quality. It is a smart investment to increase production, reduce waste, and achieve maximum efficiency.
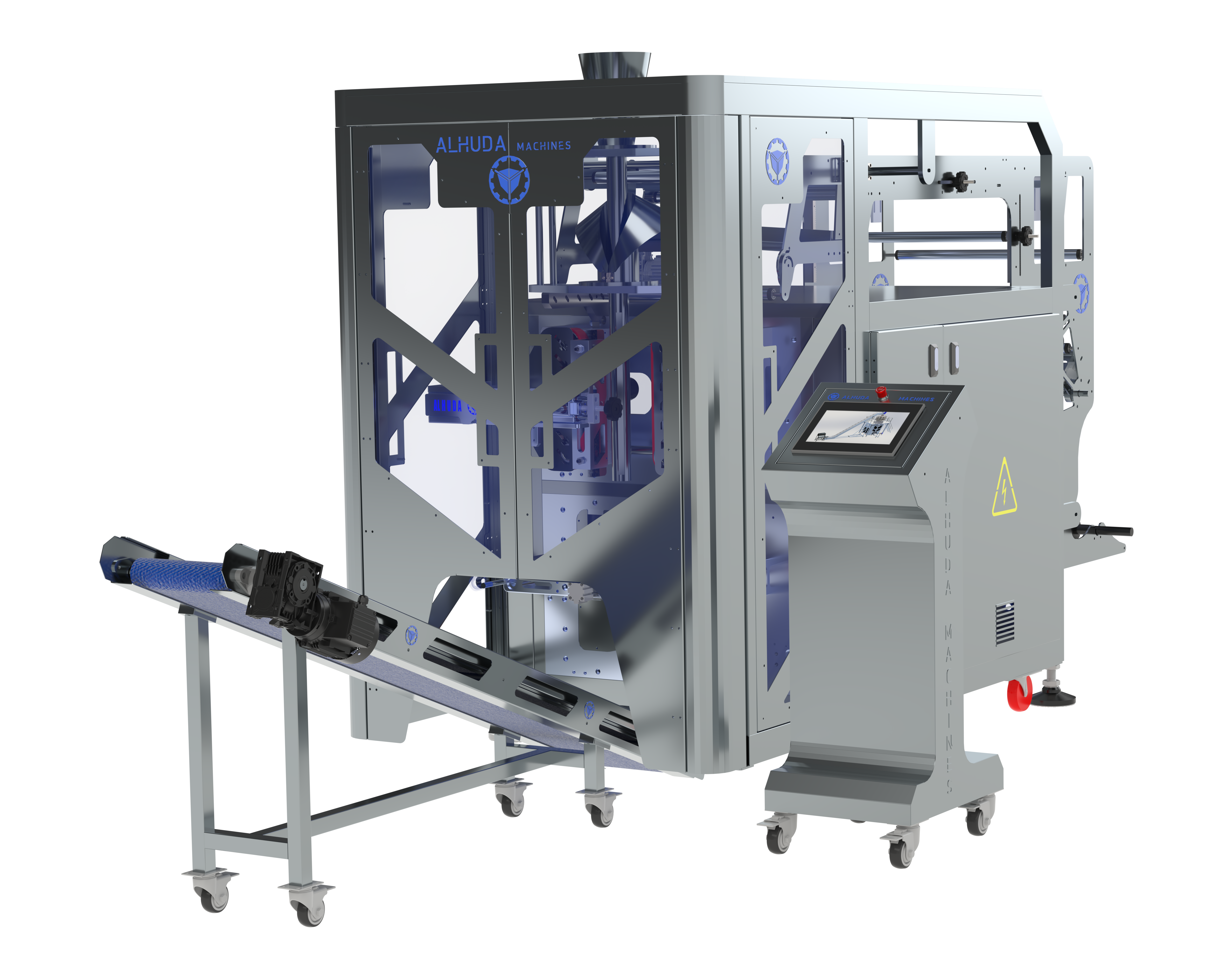
The platform supporting the weighing tower
🔹 The industrial platform, specifically designed to support the multi-head weighing tower, is an essential component of precision packaging systems. The scale unit is mounted on top of it to accurately measure materials before packaging.
🔍 Detailed Platform Description:
✅ Main Function: This platform provides a solid and secure base for the installation of the electronic multi-head weighing tower, ensuring the stability of the unit during operation and preventing any vibration that could affect weighing accuracy.
✅ Structural Design: ▪ Made of treated industrial steel or food-grade stainless steel (upon request).
▪ A non-slip mesh base allows for excellent ventilation and easy cleaning.
▪ Protective handrails around the entire perimeter enhance safety during operation.
▪ A metal side step for easy access and safe ascent to the platform.
✅ Durability: ▪ Thoughtfully engineered to withstand heavy loads.
▪ Reinforced corner supports provide additional stability during operation.
✅ Uses: ▪ Food packaging lines (chips, legumes, frozen foods, and granules).
▪ Suitable for all types of multihead weighers.
🔒 Additional Features: ▪ High operator safety.
▪ Easy installation and compatible with most production lines.
▪ Available in various sizes according to factory requirements.
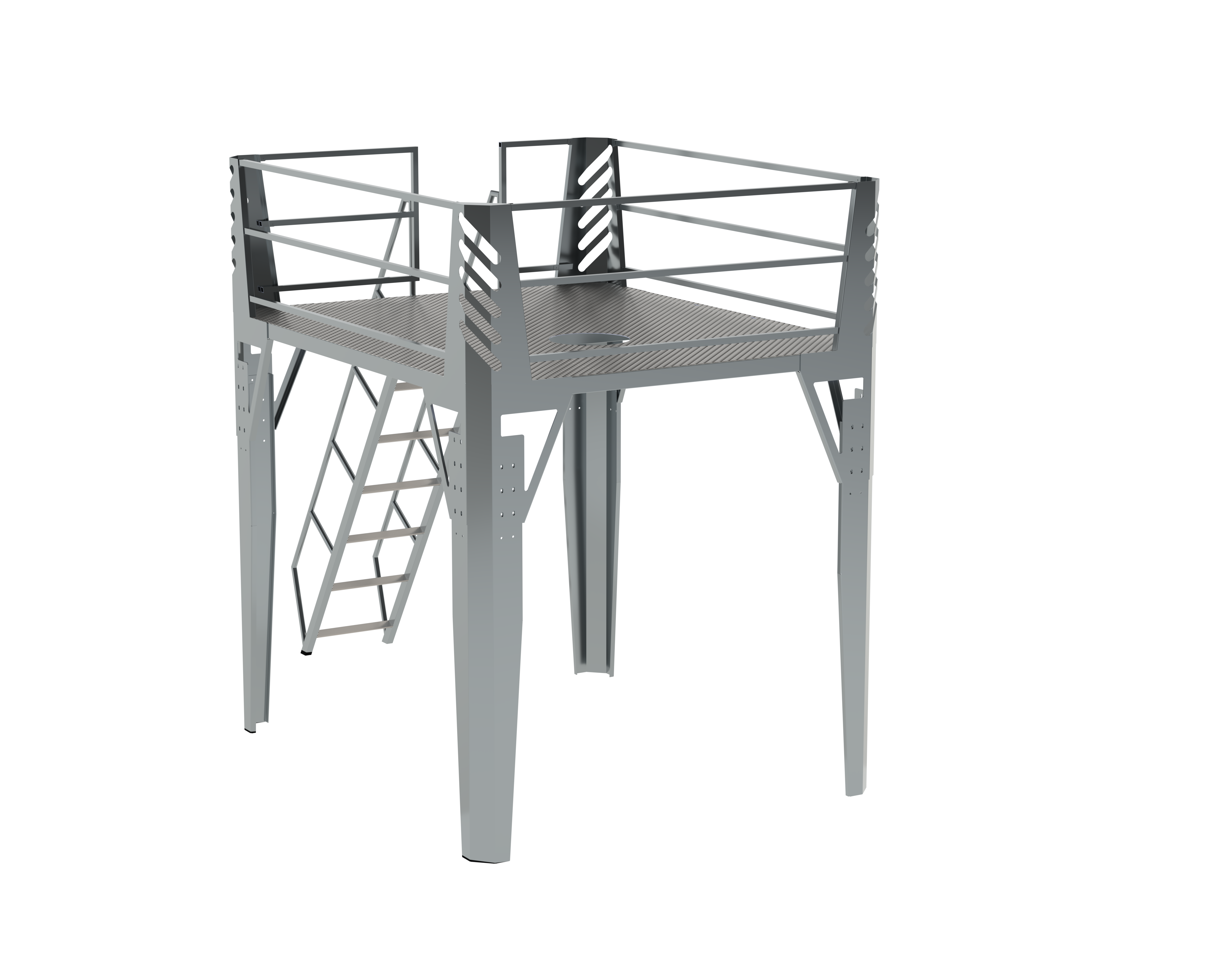
Libra the multi-headed
⚖️🔹 This tower is one of the most important components of modern packaging lines. It weighs materials with extreme precision and at high speeds, providing reliable and balanced performance in all packaging operations, especially when packaging light products such as potato chips and corn.
🔍 Detailed explanation of the scale:
✅ Main function:
Automatically measures product weight using a multi-scale system that ensures the highest degree of weight accuracy, even with heterogeneous or unevenly sized materials.
✅ Types of scales available and their performance in packaging chips:
▪️ 10 heads (buckets):
▫️ Weighs approximately 65 packets per minute, up to 75 packets per minute depending on the desired packaging weight.
▪️ 14 heads:
▫️ Weighs approximately 85 packets per minute, up to 95 packets per minute depending on the weight.
▪️ 16 Heads:
▫️ Weighs approximately 100 envelopes per minute, up to 120 envelopes per minute.
▪️ 20 Heads:
▫️ Weighs approximately 120 envelopes per minute, up to 150 envelopes per minute, making it the ideal choice for very large-volume production lines.
✅ Tower Features:
▪️ 12-inch smart touchscreen control panel.
▪️ Multilingual software system (Arabic, Turkish, and English).
▪️ Adjustable weight to suit the product within a range of 10–1000 grams.
▪️ Ergonomic design for easy access to parts for maintenance and cleaning.
▪️ Equipped with a memory to store more than 100 different filling programs.
▪️ Advanced dispensing algorithm to ensure the highest accuracy with minimal waste.
✅ Common Uses:
Used for packaging:
– Potato and corn chips
– Legumes and grains
– Nuts
– Sweets and confectionery
– Frozen products
🔒 Quality Manufacturing:
Turkish-made with European technology, manufactured from food-grade 304 stainless steel, resistant to rust and corrosion, and designed to withstand long hours of continuous operation without compromising performance.
📌 Choose the scale that's right for your factory from a full range of 10, 14, 16, and 20 heads, all available with us.
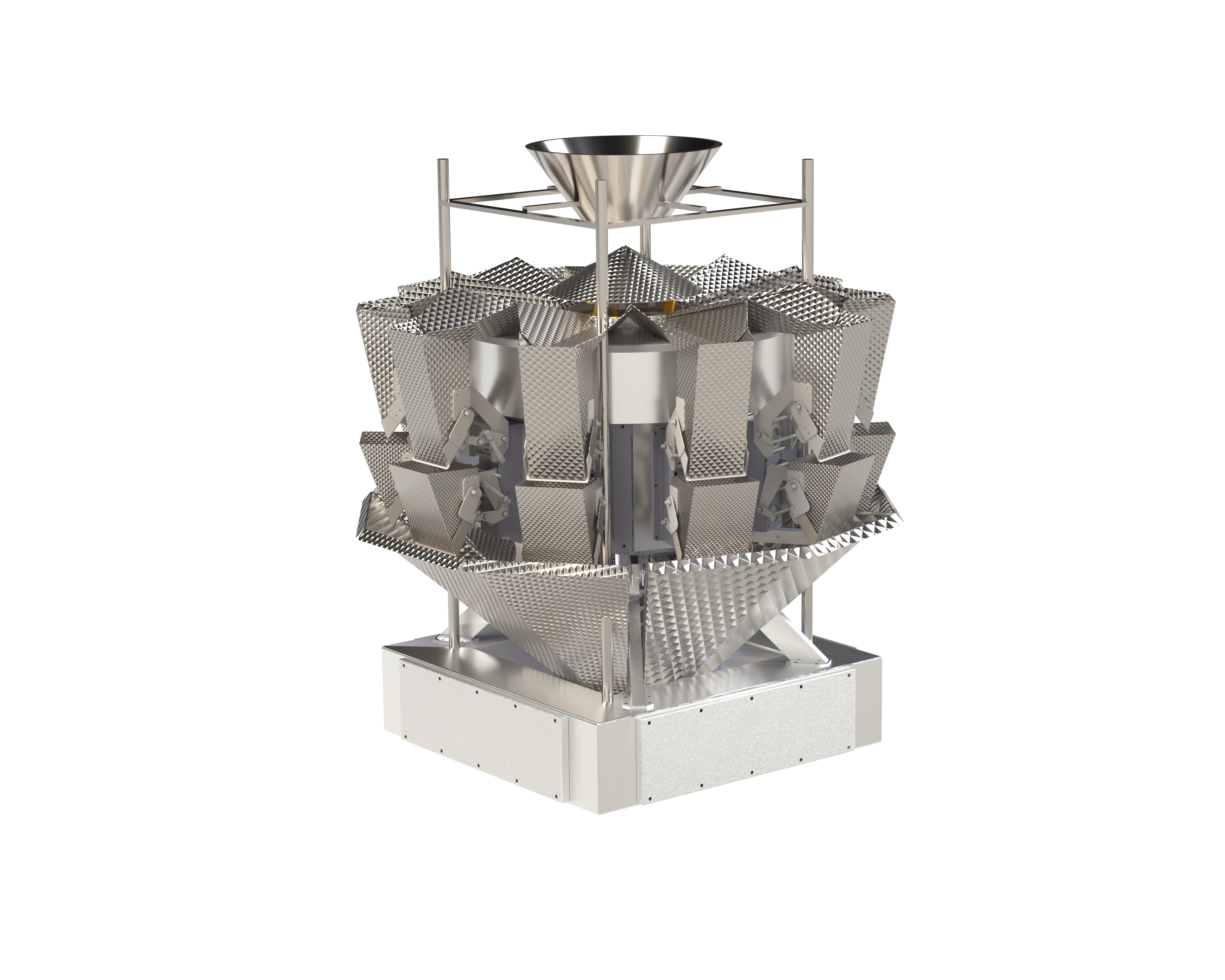
Conveyor belt feeding the packaging machine
🔹 General Function: The feeding conveyor is one of the most important components in packaging lines, transporting food materials in a continuous and uniform manner from the automated feeder to the packaging machine. This conveyor is characterized by its high precision and smooth operation, ensuring continuous and consistent feeding without interruption.
🔍 Detailed Explanation of Operation:
1. ✅ The body is made entirely of food-grade 304 stainless steel to ensure rust resistance, ease of cleaning, and full compliance with health standards.
2. ✅ Mechanical Operating System:
▪️ Equipped with a motor for precise transmission and smooth performance.
3. ✅ The conveyor belt is equipped with blades (barriers) to stabilize materials during ascent and prevent slippage, even when used with granular or light materials such as chips, sugar, nuts, and legumes.
4. ✅ Mobile Design:
▪️ Equipped with swivel wheels with brakes for easy transportation and stability during operation.
5. ✅ Precise electronic control: Can be connected to an electronic control panel or PLC system to adjust the conveyor speed and feeding timing to match the speed of the packaging machine.
📐 Technical Specifications:
Material: 304 food-grade stainless steel
Motor type: GAMAK – Turkey
Gearbox: VARVEL – Italy
Electrical power: As requested – starting from 0.75 kW
Conveyor belt type: food-grade PVC, resistant to friction and wear
Total length: As requested
Width: Customized according to the packaging machine inlet dimensions
Movement system: Internal chains or industrial belts
Wheel system: 4 swivel wheels with locking brakes
🟢 Common Uses:
▪️ Chip production lines of all kinds
▪️ Packaging of legumes, nuts, sugar, and rice
▪️ Food factories
▪️ Automatic packaging lines
✨ Why choose this conveyor? Combining durability, precision, and ease of operation, it is specifically designed to integrate seamlessly with packaging machines, increasing line efficiency and reducing waste and downtime.
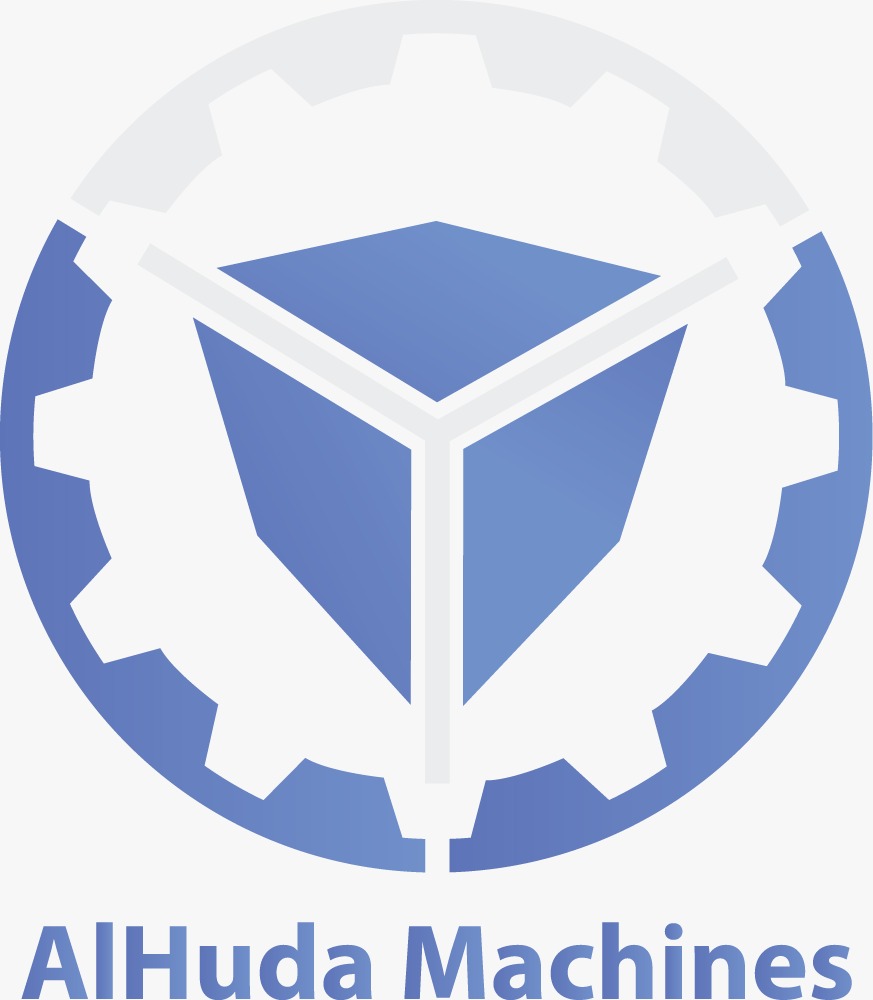
Feed shaker - with collection basin
🔹 General Function: The Feeding Hopper Vibrator is a key unit in conveying and feeding systems. It acts as an intermediate reservoir for collecting raw materials and ensuring their consistent feeding to the conveyor belt and the next machine on the production line.
🔍 Detailed Explanation of How It Works:
1. ✅ Robust and Rust-Resistant Construction: Made entirely of food-grade 304 stainless steel, ensuring the highest levels of durability, ease of cleaning, and corrosion resistance in humid working environments.
2. ✅ Inclined (hopper) design with bottom feeding ports: Helps ensure smooth material discharge without clumping, maintaining uninterrupted production flow.
3. ✅ Vibration Motor System:
▪️ Equipped with an industrial vibration motor that generates gentle, regular vibrations that help ensure efficient material flow without clogging or blockage.
▪️ Vibration intensity can be controlled according to the type of material and its viscosity or lightness.
4. ✅ Stable structure with swivel wheels: For easy transportation within the laboratory, the wheels can be locked in place during operation to ensure stability.
5. ✅ Easy maintenance and cleaning: An open-top design allows quick access for cleaning or inspection without disassembling complex parts.
📐 Technical Specifications:
Material: 304 food-grade stainless steel
Discharge system: Inclined - hopper with bottom opening
Vibrating motor type: Electric - 220/380V
Electrical power: 0.25 to 0.75 kW (upon request)
Bowl capacity: Customizable (100-300 liters)
Motor system: Stable with rotating wheels
High cleanability - Open and easy-access design
🟢 Common Uses:
▪️ Chip and snack production lines
▪️ Pulse, sugar, and flour packaging lines
▪️ Automatic feeding systems linked to conveyors or elevators
✨ Why is a feed vibrating unit essential in a production line? Because it ensures a steady, uninterrupted flow of raw materials and reduces stoppages caused by manual feeding or input blockages, increasing line efficiency and saving time and effort.
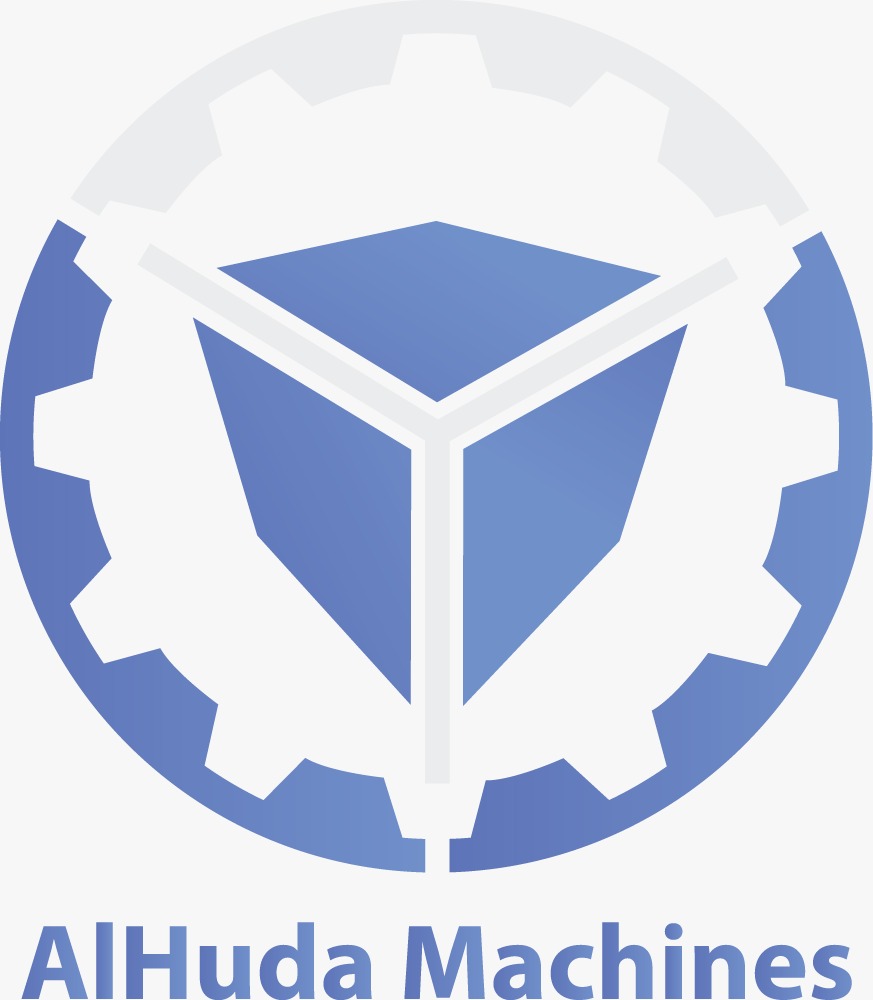
Envelope receiving flow from the packing machine
🔹 General Function: The front conveyor is used at the end of the packaging lines to receive the sealed bags or containers immediately after they exit the packaging machine, ensuring smooth transport to the assembly, inspection, or secondary packaging stage. This conveyor is essential for ensuring continuous production flow without interruption.
🔍 Detailed Explanation of How It Works:
1. ✅ Durable stainless steel construction (304 stainless steel):
▪️ Rust and corrosion resistant
▪️ Easy to clean and 100% food safe
▪️ Complies with food hygiene and safety standards
2. ✅ Inclined conveyor system:
▪️ Equipped with a high-quality PVC or PU conveyor belt
▪️ Used to convey bags in an inclined upward direction for easy manual or automatic collection
3. ✅ High-efficiency industrial drive motor
▪️ Ensures smooth movement and stable operation without vibration
4. ✅ Smart and mobile design:
▪️ Equipped with rotating wheels for easy movement within the plant
▪️ Adjustable in height and tilt angle to suit various packaging machines
5. ✅ Full integration with automatic packaging machines: Automatically connects to the end of the packaging machine to begin operation as soon as the bag is released, without the need for any manual intervention.
📐 Technical Specifications:
Material: Food-grade 304 stainless steel
Conveyor belt type: Smooth food-grade PVC or with a barrier system (upon request)
Adjustable inclination angle
Movement system: Swivel casters with locking brakes
Conveyor speed controlled via an inverter system
🟢 Common Uses:
▪️ Receiving bags of chips and crackers
▪️ Transporting packages of sugar, nuts, or legumes after packaging
▪️ Various food production lines
▪️ Collection points or packaging lines
✨ Why do you need this conveyor in your production line? Because it provides complete continuity, prevents bag stacking at the exit of the packaging machine, and facilitates handling and final assembly, saving time and increasing production efficiency.
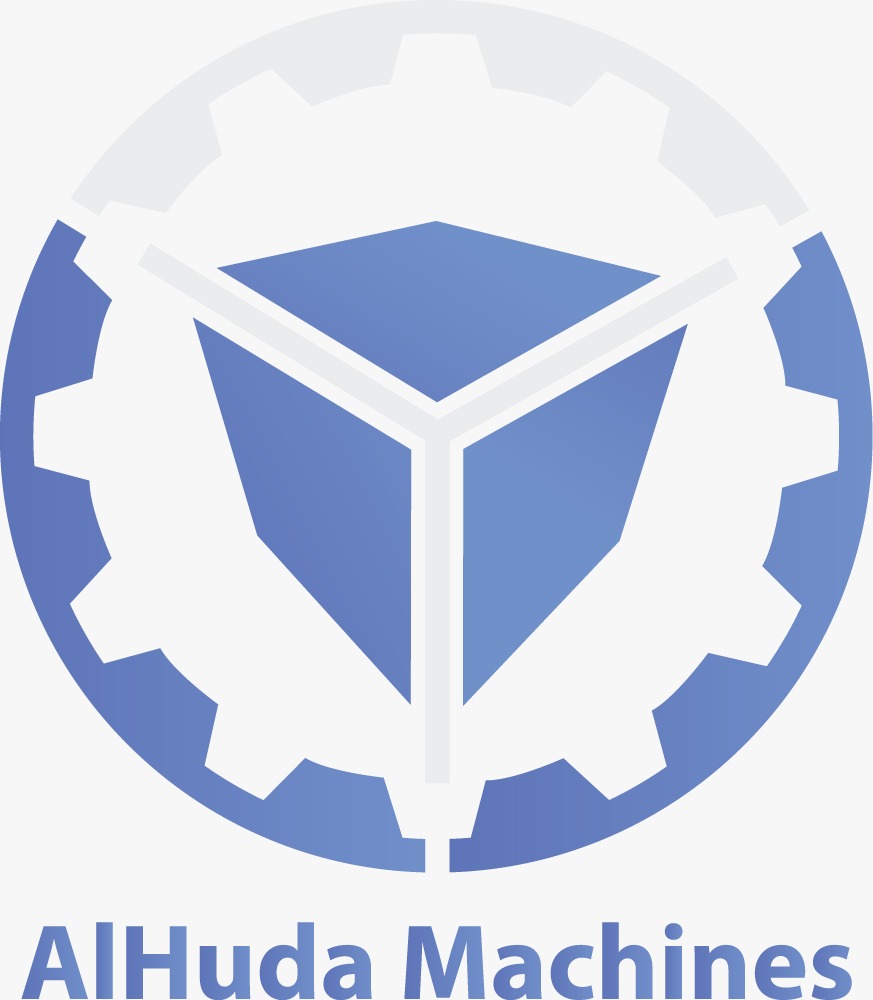
Rotary table - finished product collection tray
🔹 General Function: The rotary table is used at the end of packaging lines to collect bags or sealed packages after they exit the final conveyor. This unit is ideal for automatically arranging products in a circular manner, making it easier for workers to pick them up for packaging into cartons or transport to the next stage.
🔍 Detailed Explanation of How It Works:
1. ✅ Hygienic and Durable Design:
▪️ Made entirely of stainless steel (304 stainless steel)
▪️ Rust and moisture resistant and easy to clean
▪️ Smooth rotating surface ensures smooth product movement
2. ✅ Automatic Rotation System:
▪️ Rotates smoothly and steadily to ensure the order of bags coming out of the packaging machine
▪️ Suitable rotation speed for easy manual handling of products
3. ✅ Increased Productivity and Reduced Waste:
▪️ Organizes the bag collection process and prevents bag accumulation or falling
▪️ Facilitates handling and packing into cartons or boxes
4. ✅ Safe and Ergonomic Design:
▪️ Suitable height for operator comfort
▪️ Rounded corners to ensure safety during operation
📐 Technical Specifications:
Valuable Specification
Material: Food-grade 304 stainless steel
Movement Type: Continuous Circular Motion
Standard Table Diameter: 100 to 120 cm (depending on the size of the table) (Request)
Height adjustable according to the location of use
Power supply: 220/380V - 50/60Hz
Speed control available (optional via inverter)
🟢 Common uses:
▪️ Chip and cracker packaging lines
▪️ Sugar, legume, and nut bag collection
▪️ Food, pharmaceutical, and spice factories
▪️ Fully automatic packaging systems
✨ Why choose a rotary table at the end of the production line? Because it ensures perfect and smooth organization of the finished products, facilitating manual or automatic work, increasing assembly speed and packaging accuracy, and thus increasing production line efficiency.
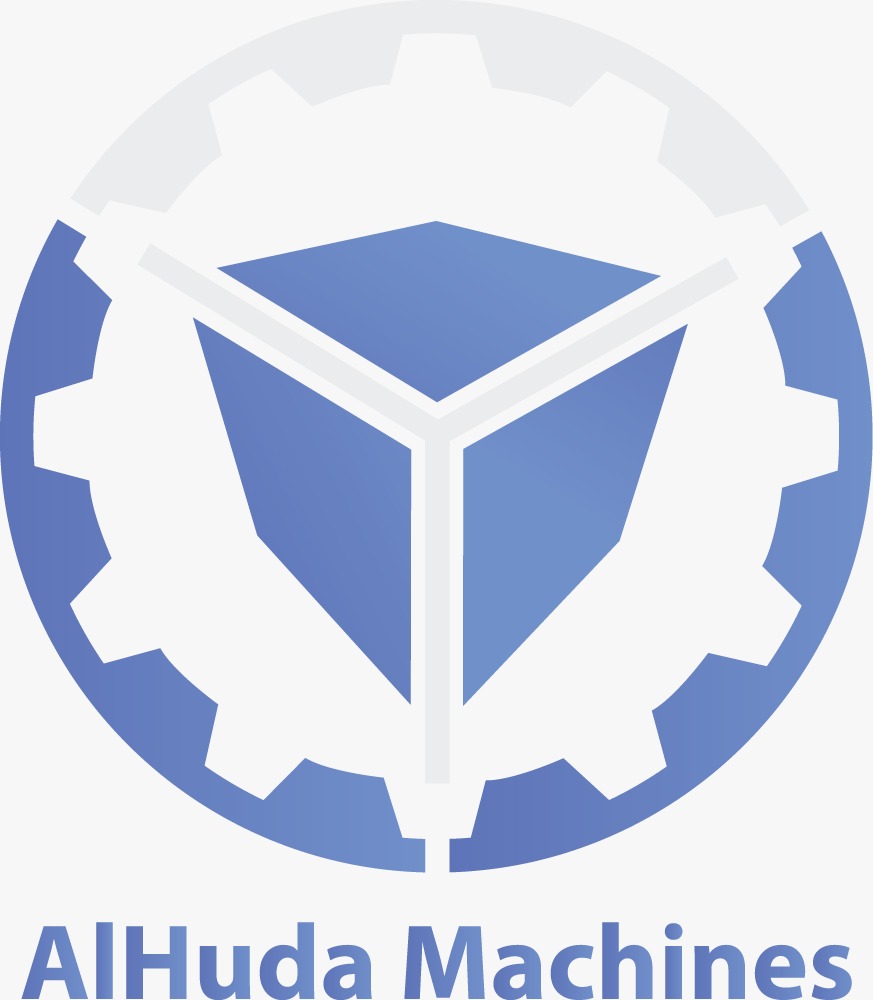
Digital Date Printer - (Optional Unit)
🔹 General Function: The digital date printer is an important add-on unit that can be integrated with packaging machines. It is designed to print production and expiration dates, barcodes, batch numbers, and logos on various packaging materials.
🔍 Detailed Explanation of How It Works:
1. ✅ Direct Installation on the Packaging Machine: The printer is mounted on the film conveyor in the packaging machine to automatically print on each bag during manufacturing.
2. ✅ Accurate and Clear Printing: This unit provides thermal or inkjet printing, depending on the type, and is used to print fixed or variable markings (such as dates or serial numbers).
3. ✅ Suitable for various packaging types:
▪️ Plastic (OPP – BOPP – PE)
▪️ Paper – Aluminum – Metallic Foil
▪️ Flexible and transparent containers
4. ✅ Easily programmable and adjustable:
▪️ Text input and settings can be adjusted via a touch screen control panel
▪️ Supports printing on the packaging line at high speeds without compromising performance
🛠️ Important Note:
🔺 This unit is optional and not mandatory within the line, but it is highly recommended, especially in food, spice, nut, or pharmaceutical packaging lines, to comply with quality and health control requirements.
🧩 Types of Date Printers Available: There are a large number of types of date printers available depending on the type of project and the materials used, including:
Type of Printer Operation Main Feature
Thermal Printer: Printing using heat on a special ribbon, economical and fast.
Jet Printer: High-resolution on various surfaces.
Laser Coding Printer: Inkless, laser-based, high-resolution, suitable for high speeds.
Ribbon Printer: Printing ribbons during bag packaging. Accurate and consistent printing.
🟢 Key Benefits:
▪️ Compliance with food and health standards.
▪️ Accurate product tracking via batch codes.
▪️ Preventing fraud and forgery and ensuring transparency.
▪️ Improving the appearance of the final product and enhancing consumer confidence.
✨ Do you need a printer for your project? If you work in the food, spice, pharmaceutical, or any product sector that requires an expiration date or batch number, using a date printer is an essential option to ensure product quality and customer confidence.
1751653869_3.jpeg)
control Board
• SCHNEIDER Cutters
• SCHNEIDER CONTACTERS
• 10 inch DELTA control screen
• Inverters DELTA
• Engines, the Turkish company GAMAK, with a German franchise
• Gearboxes of the famous Turkish brand YILMAZ
• According to the client's request
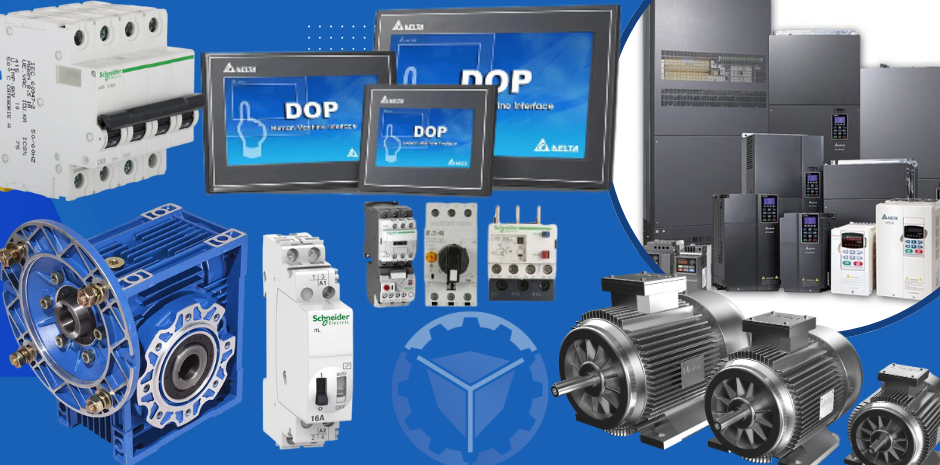
basic information
Turkish industry with German technology spanning more than twenty years
Our industries have international quality certificates
Al-Huda is the experience of generations in the world of industry, creativity of the era and development towards the future
Made of food grade chromium 304
Learn more about our 14 scale weighing packaging machine
Request a quote
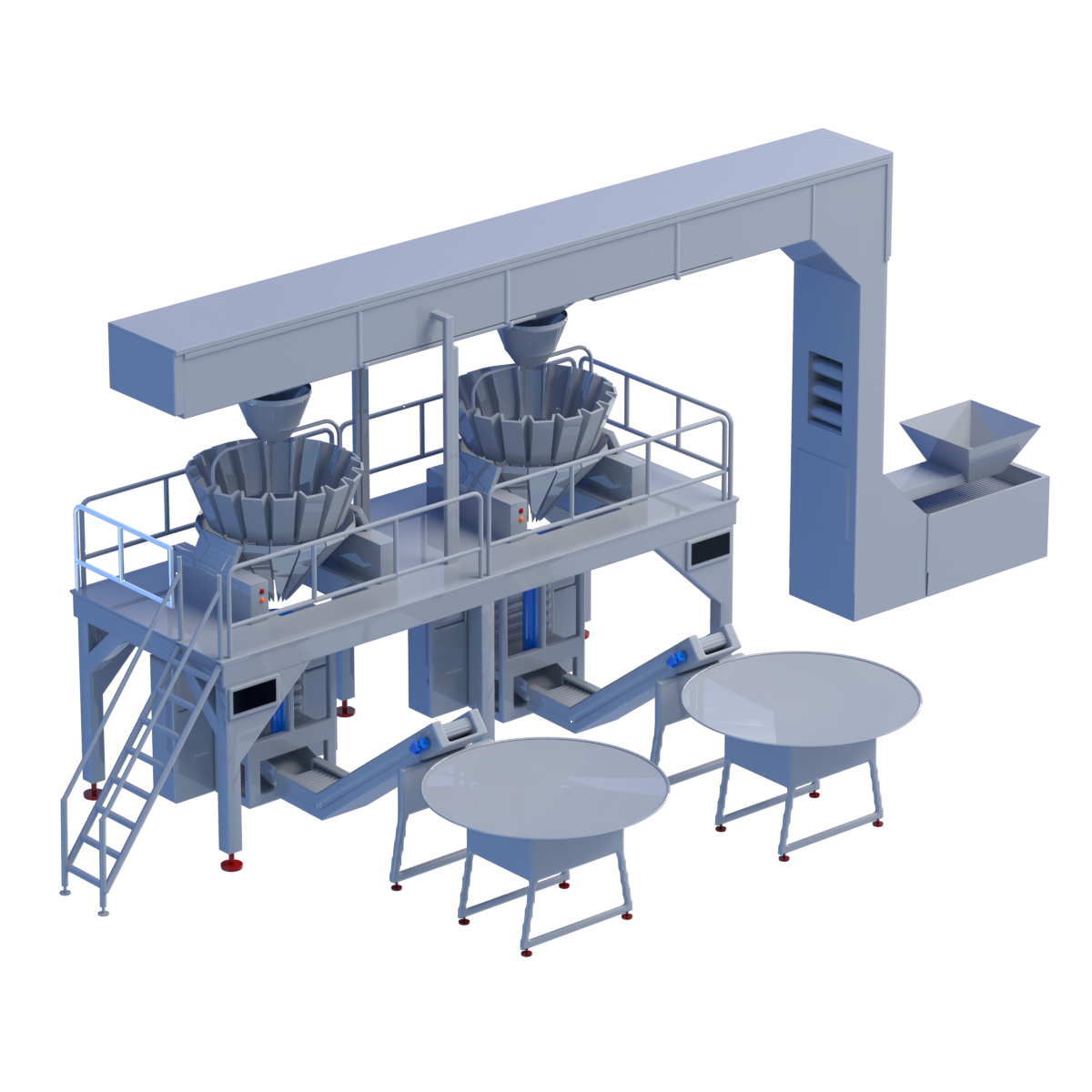
Chips types
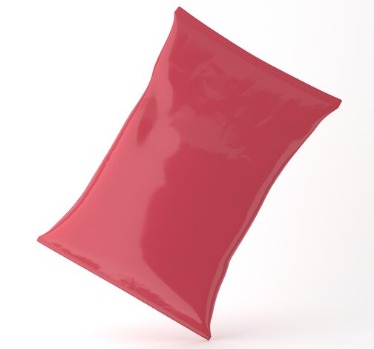
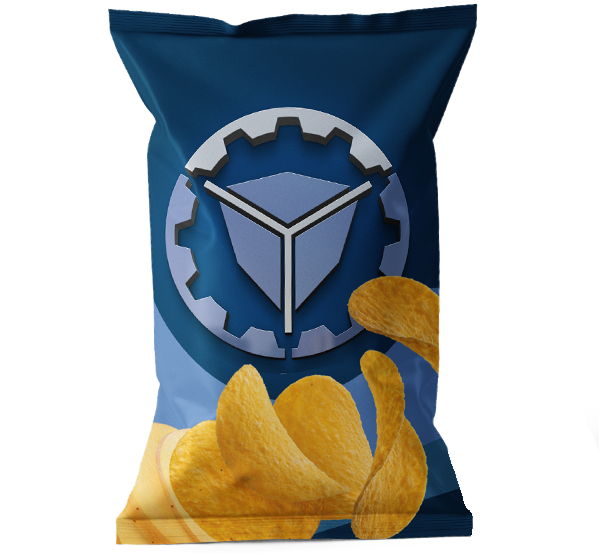
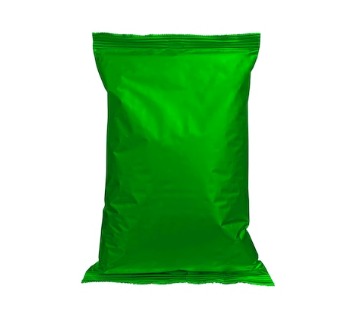
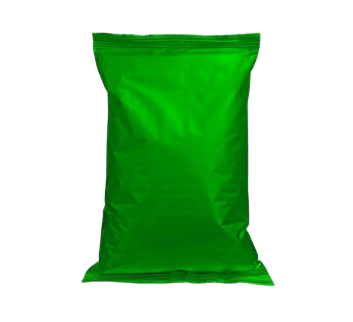
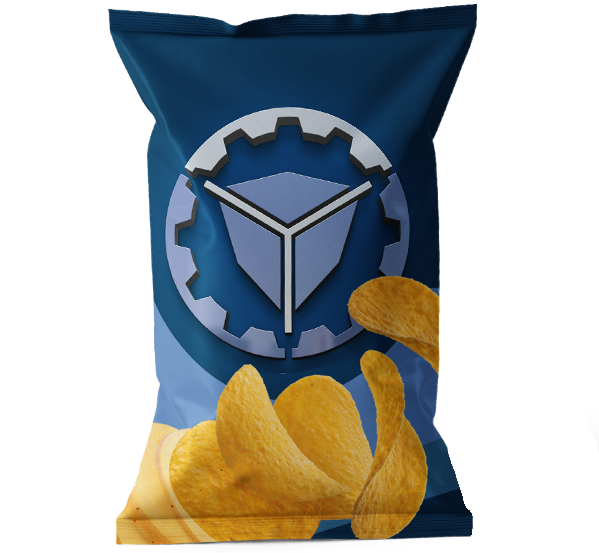